BMW considers it crucial to reduce the use of primary raw materials. Because the process to obtain secondary materials is much less harmful to the environment and generates much less CO2 emissions than the intensive mining and processing of raw materials.
CIRCULARITY
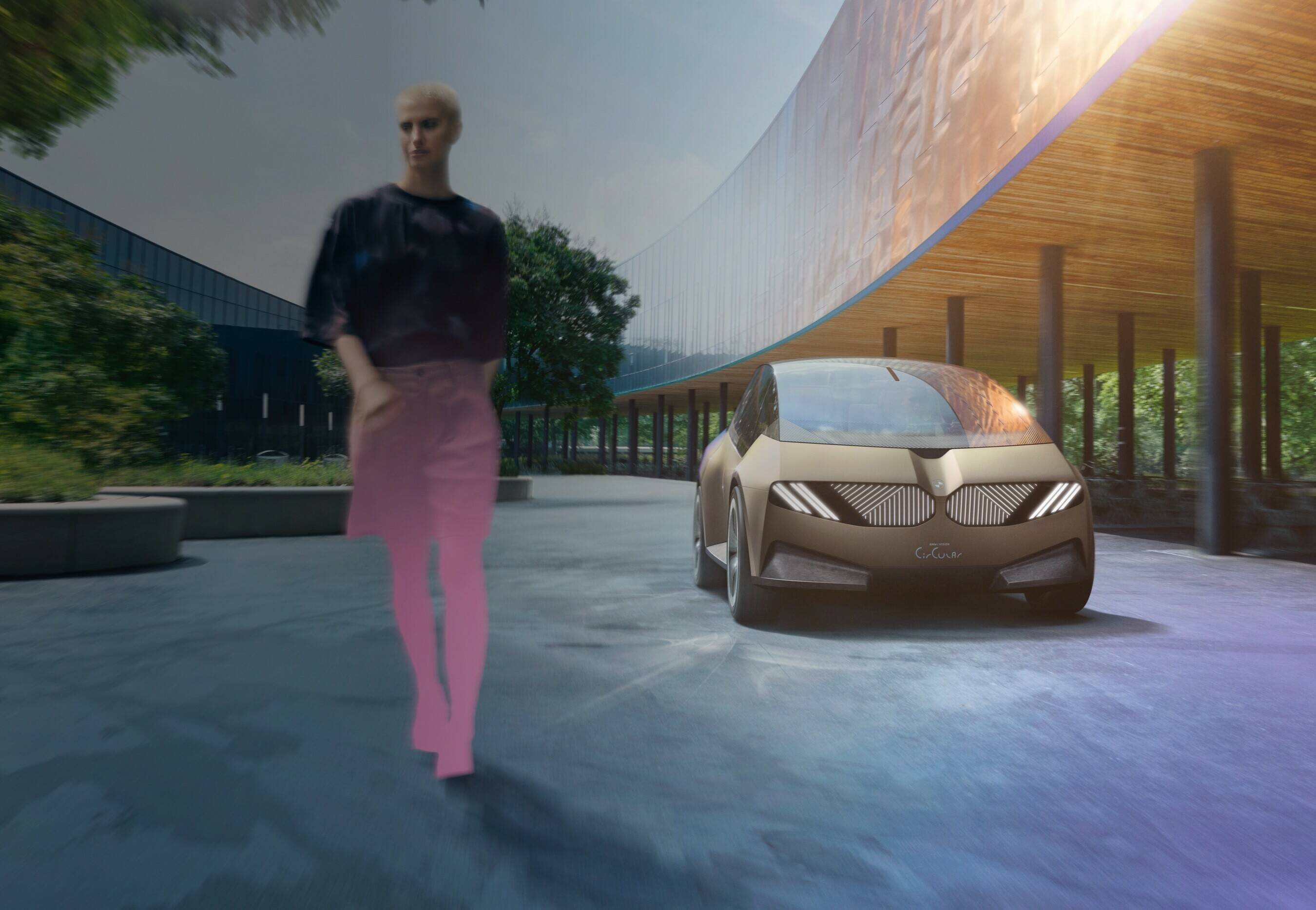

Where can we reduce the use of materials? Which materials can we reuse?
We will significantly increase the share of secondary materials in our vehicles.
In the coming years from – already – 30% to 50%. Secondary First.
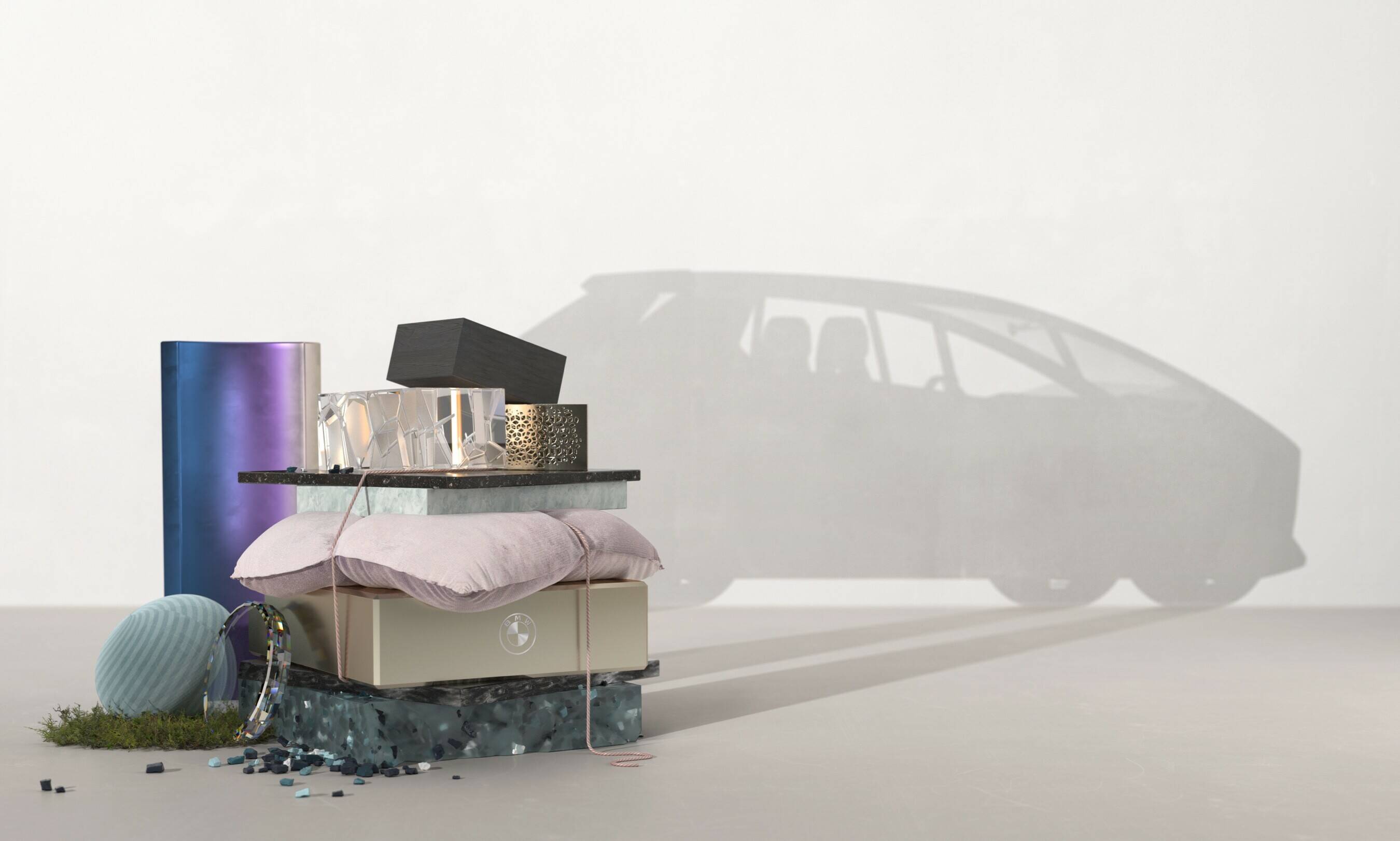
The BMW i Vision Circular is our vision for the year 2040. 100% circular design. For example with secondary aluminum and steel, obtained by recycling waste materials. Colored by heating instead of lacquer.
With 3D printed parts, recycled plastic and recycled rubber.

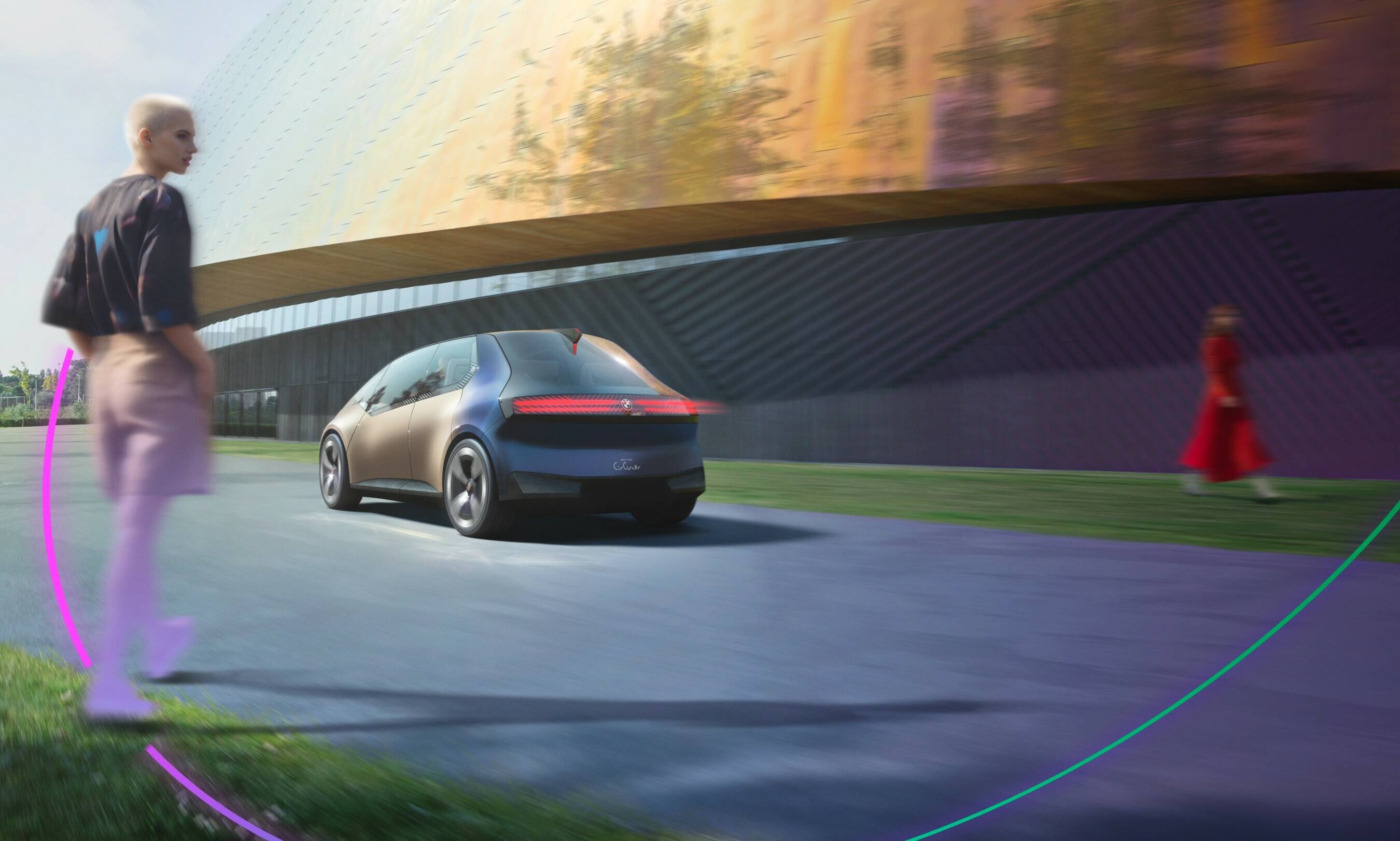
Circular use of materials already plays an important role in current models. The BMW iX, for example, already uses 60 kilograms of recycled plastic, as well as recycled aluminum, seat covers made of natural wood fiber and floor mats made of recycled fishing nets.

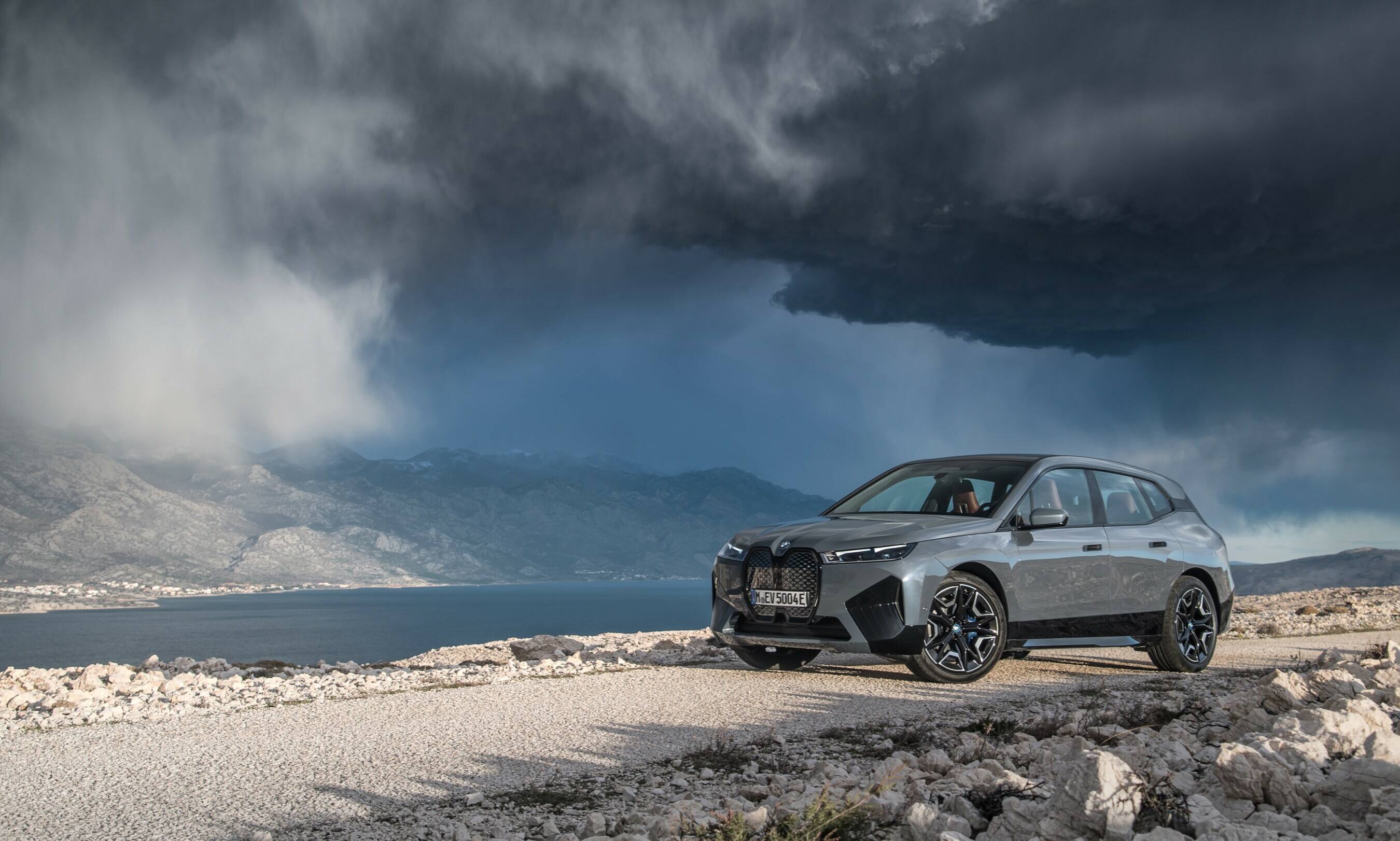
A SUSTAINABLE MATERIAL CYCLE FOR BATTERY CELLS
The BMW Group has set itself the goal of creating a closed and sustainable material cycle for battery cells: from material selection to composition, design, manufacturing and recycling of battery cells.

With the new pilot plant where lithium-ion battery cells are being produced, we are taking the next logical step in covering all aspects of the battery cell value chain: from selection of materials, to battery cell composition and design, through to near-standard production and recycling.

We purchase cobalt and lithium directly from the mines and deliver it to our battery manufacturer, in order to improve working conditions in these mines. To that end, we have joined forces with BASF and Samsung in the 'Cobalt for Development' project.

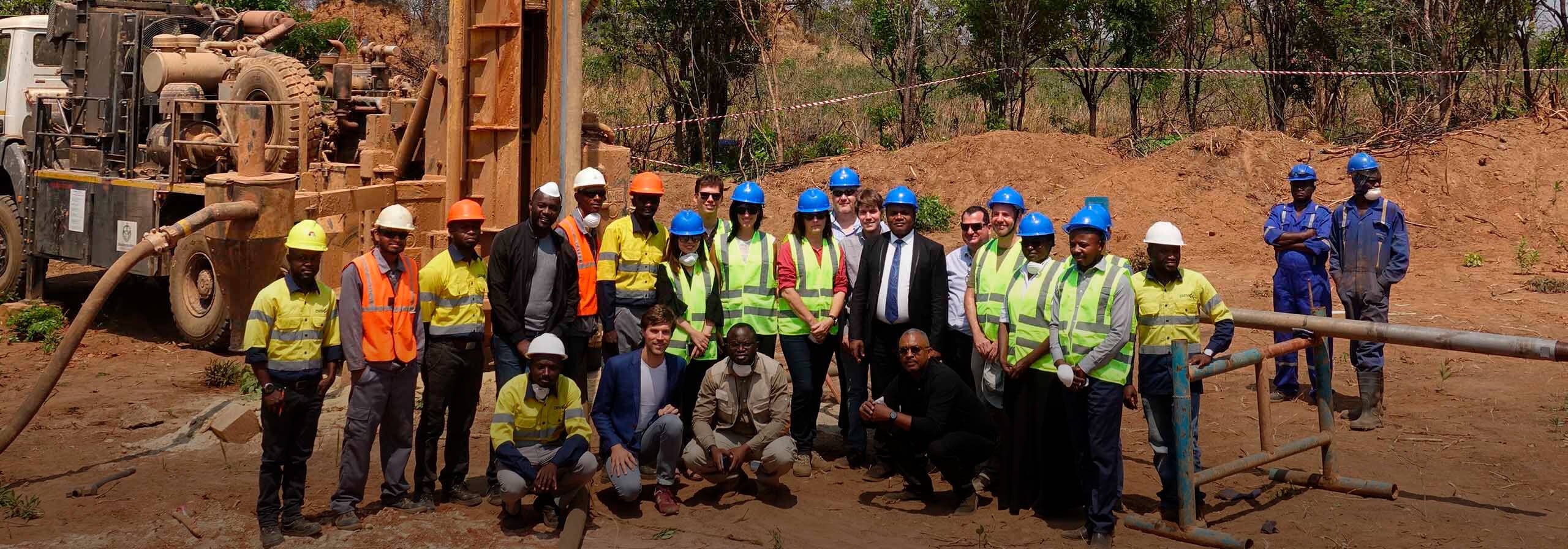

The BMW Group takes back all used BMW high-voltage batteries worldwide, even though this is not required by law. The batteries are then given a second life by using them for energy storage, before recycling them, for example at the BMW Group plant in Leipzig.
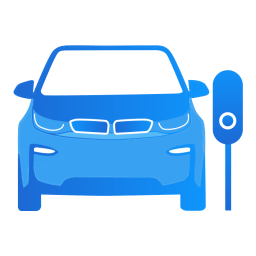

In recycling we re-use the scarce raw materials from the battery for the production of new batteries. We also use fewer and fewer rare earth elements:
THE BMW iX3 BATTERY ALREADY CONTAINS TWO-THIRDS LESS COBALT
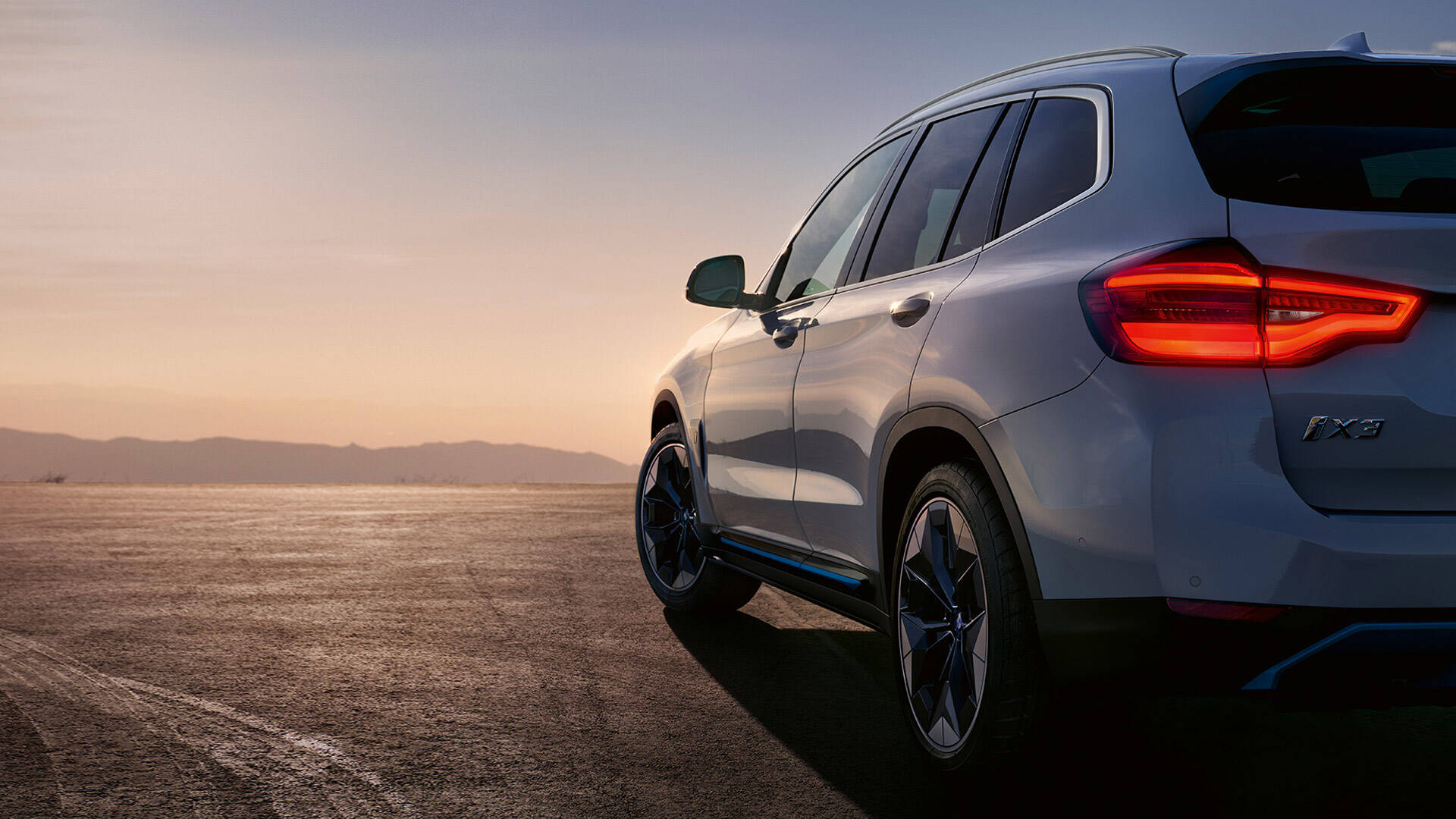
BMW
GROUP
Global production network
Fraud-proof, consistent verifiable data collection and transaction in the supply chain.
A broad variety of participants in a multi-stage international supply chain.









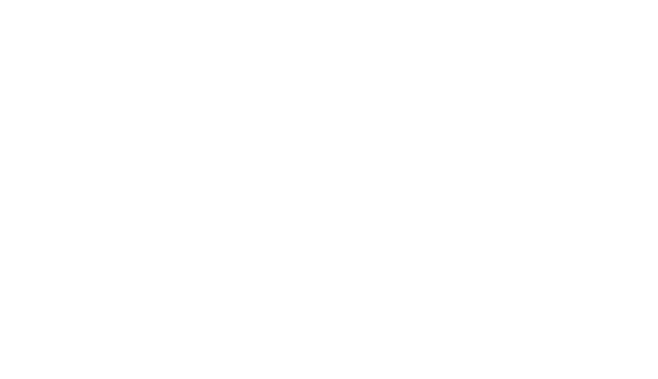

BMW Group is conducting pilot projects using digital tools, including blockchain technology, to track and control the global flow of goods.
The PartChain project, for example, makes it possible to collect supply chain data in a manner that is both consistent and fraud-proof. In the future, these digital technologies will enable us to track critical raw materials from source to reuse.
BLOCKCHAIN

We want to create transparency in recycling and reduce the usage of so-called virgin materials by re-using them on a large scale.
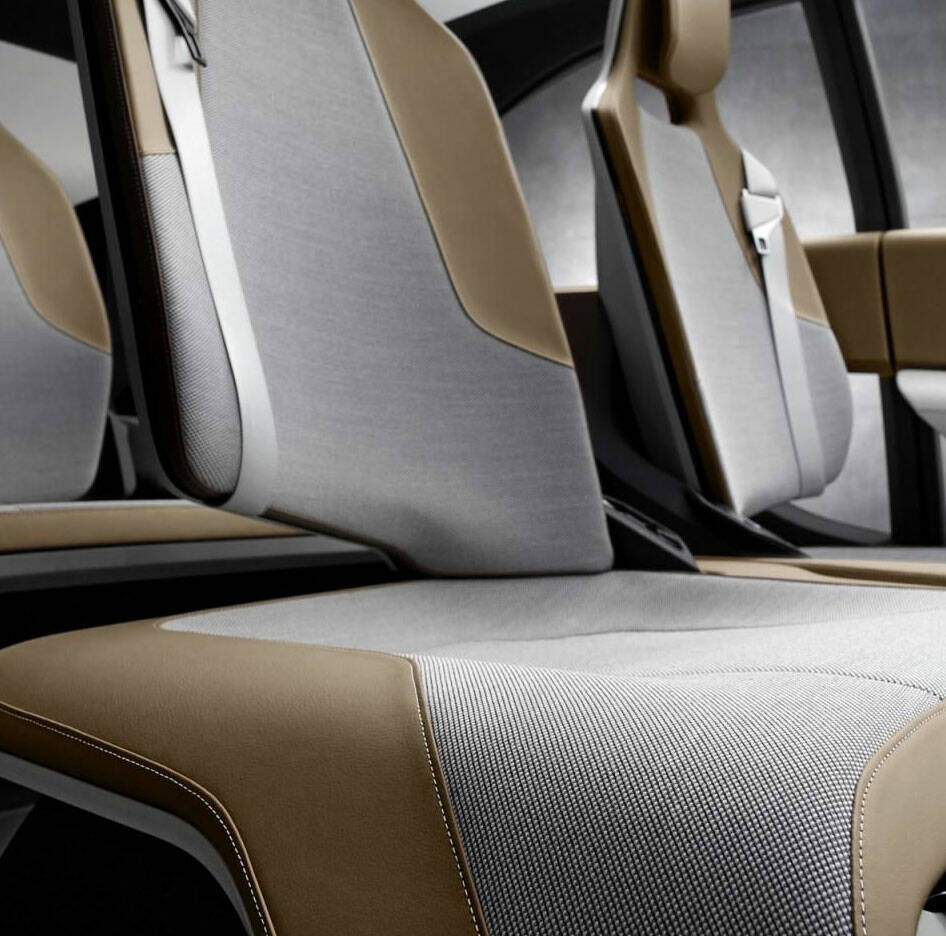
BMW considers it crucial to reduce the use of primary raw materials. Because the process to obtain secondary materials is much less harmful to the environment and generates much less CO2 emissions than the intensive mining and processing of raw materials.
CIRCULARITY
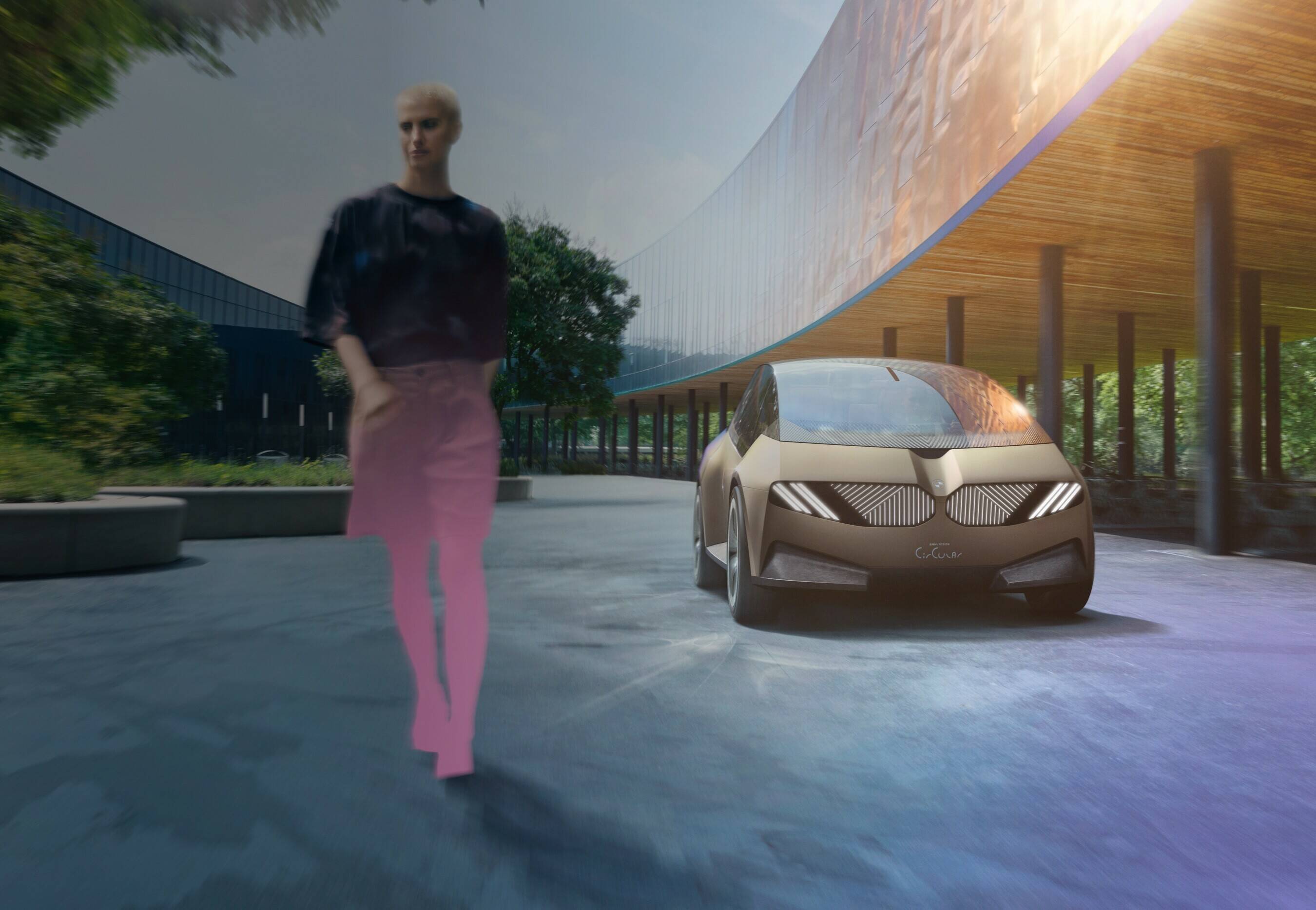
Where can we reduce the use of materials? Which materials can we reuse?
We will significantly increase the share of secondary materials in our vehicles.
In the coming years from – already – 30% to 50%. Secondary First.
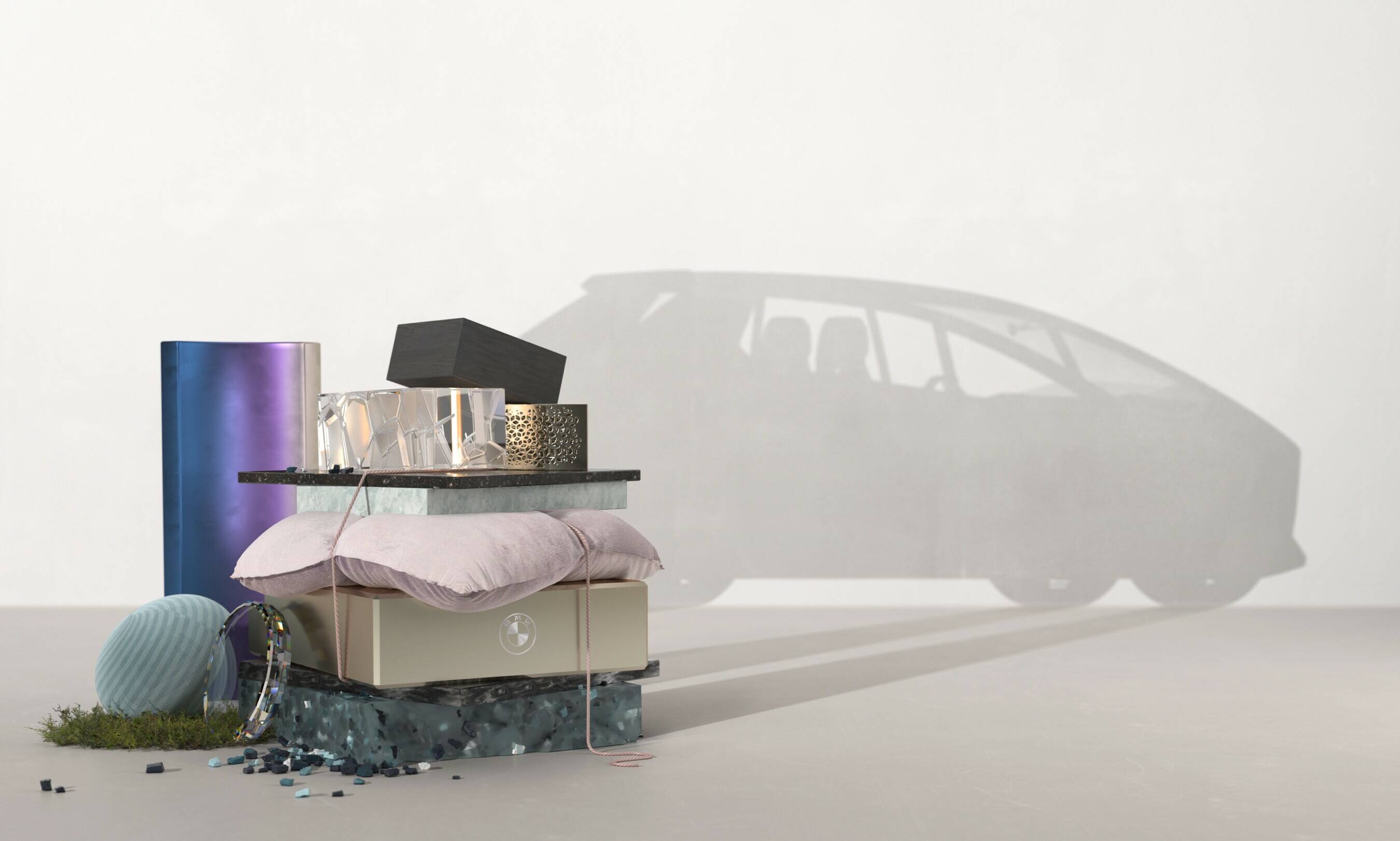
The BMW i Vision Circular is our vision for the year 2040. 100% circular design. For example with secondary aluminum and steel, obtained by recycling waste materials. Colored by heating instead of lacquer.
With 3D printed parts, recycled plastic and recycled rubber.
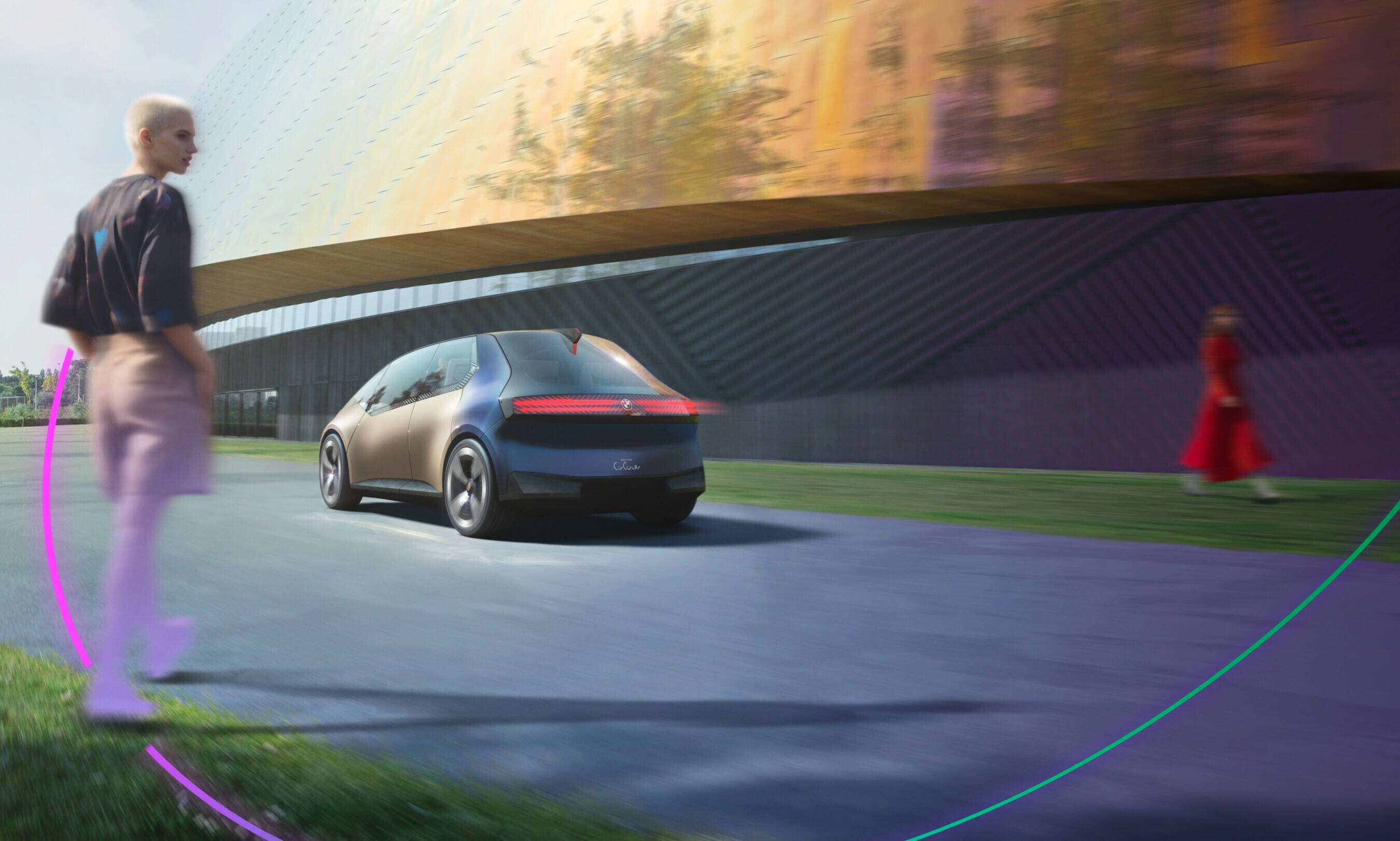
Circular use of materials already plays an important role in current models. The BMW iX, for example, already uses 60 kilograms of recycled plastic, as well as recycled aluminum, seat covers made of natural wood fiber and floor mats made of recycled fishing nets.
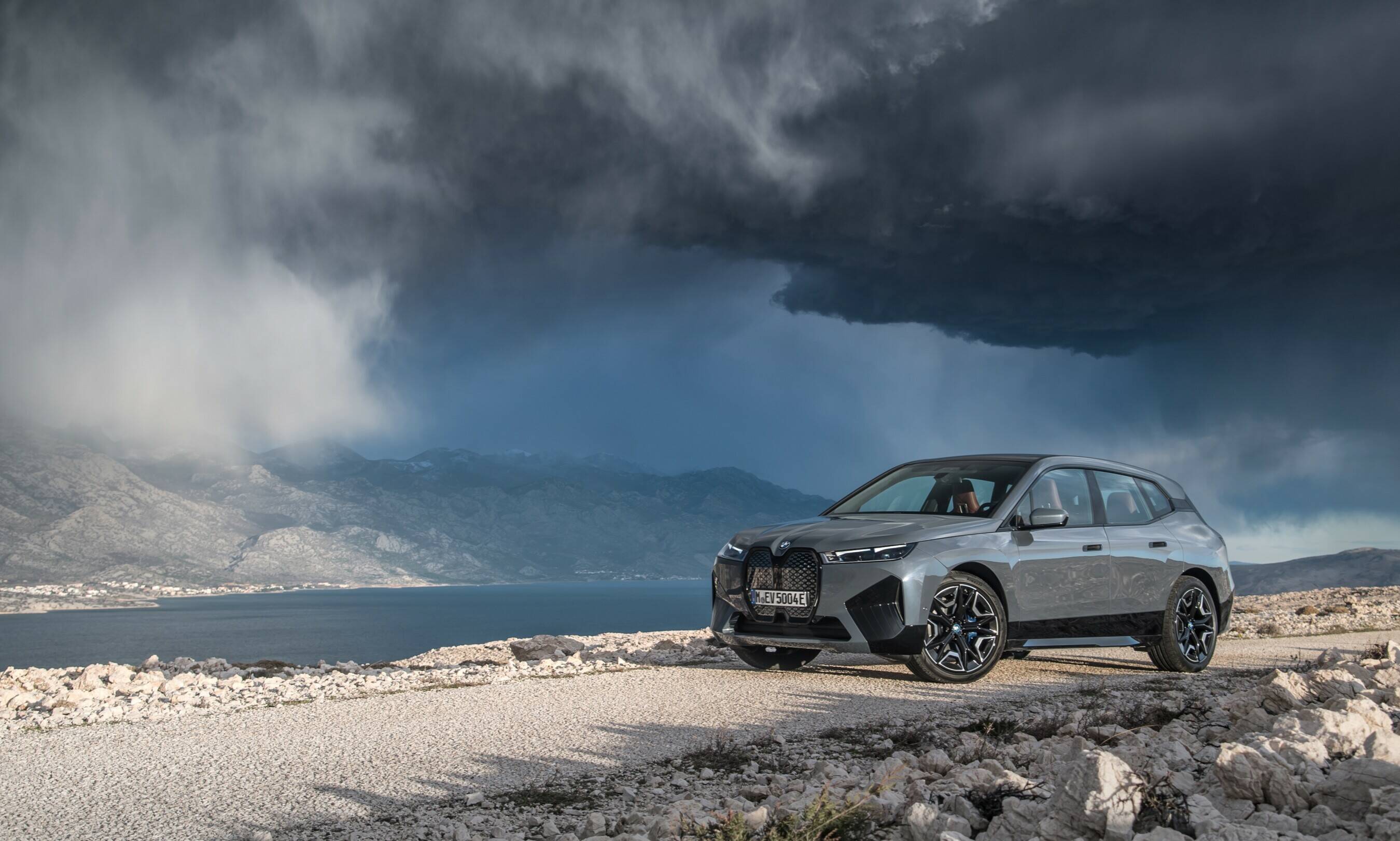
A SUSTAINABLE MATERIAL CYCLE FOR BATTERY CELLS
The BMW Group has set itself the goal of creating a closed and sustainable material cycle for battery cells: from material selection to composition, design, manufacturing and recycling of battery cells.
With the new pilot plant where lithium-ion battery cells are being produced, we are taking the next logical step in covering all aspects of the battery cell value chain: from selection of materials, to battery cell composition and design, through to near-standard production and recycling.
We purchase cobalt and lithium directly from the mines and deliver it to our battery manufacturer, in order to improve working conditions in these mines. To that end, we have joined forces with BASF and Samsung in the 'Cobalt for Development' project.
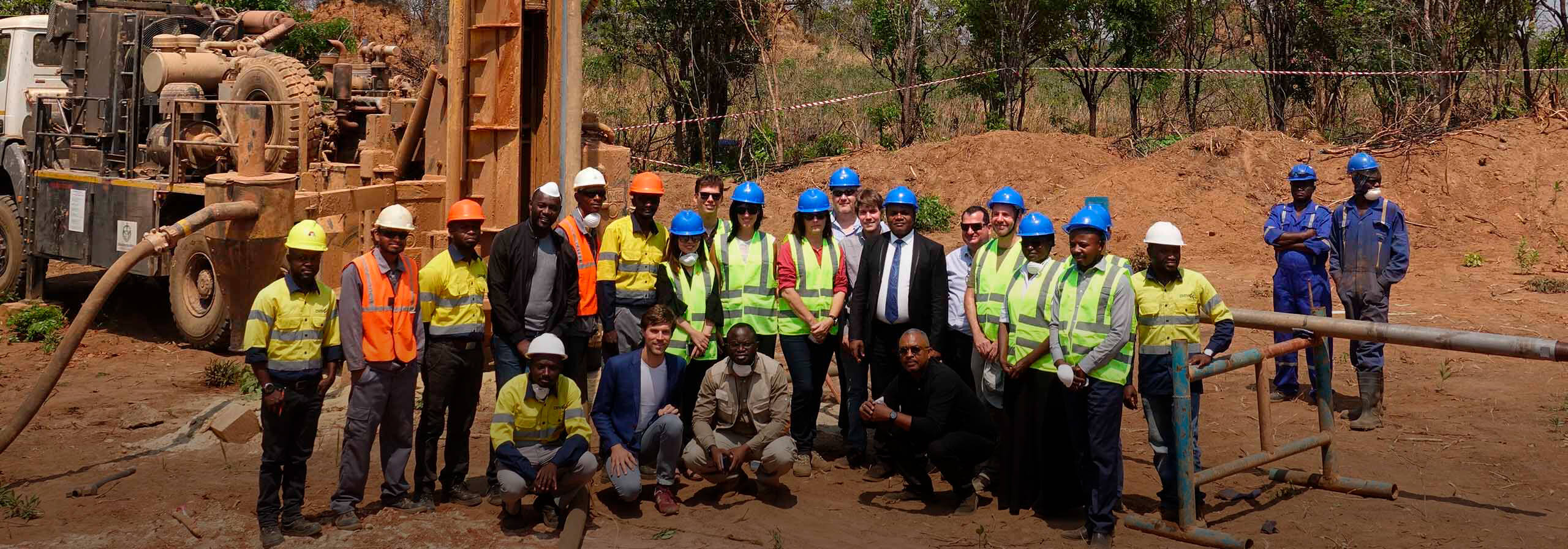
The BMW Group takes back all used BMW high-voltage batteries worldwide, even though this is not required by law. The batteries are then given a second life by using them for energy storage, before recycling them, for example at the BMW Group plant in Leipzig.
In recycling we re-use the scarce raw materials from the battery for the production of new batteries. We also use fewer and fewer rare earth elements.
THE BMW iX3 BATTERY ALREADY CONTAINS TWO-THIRDS LESS COBALT
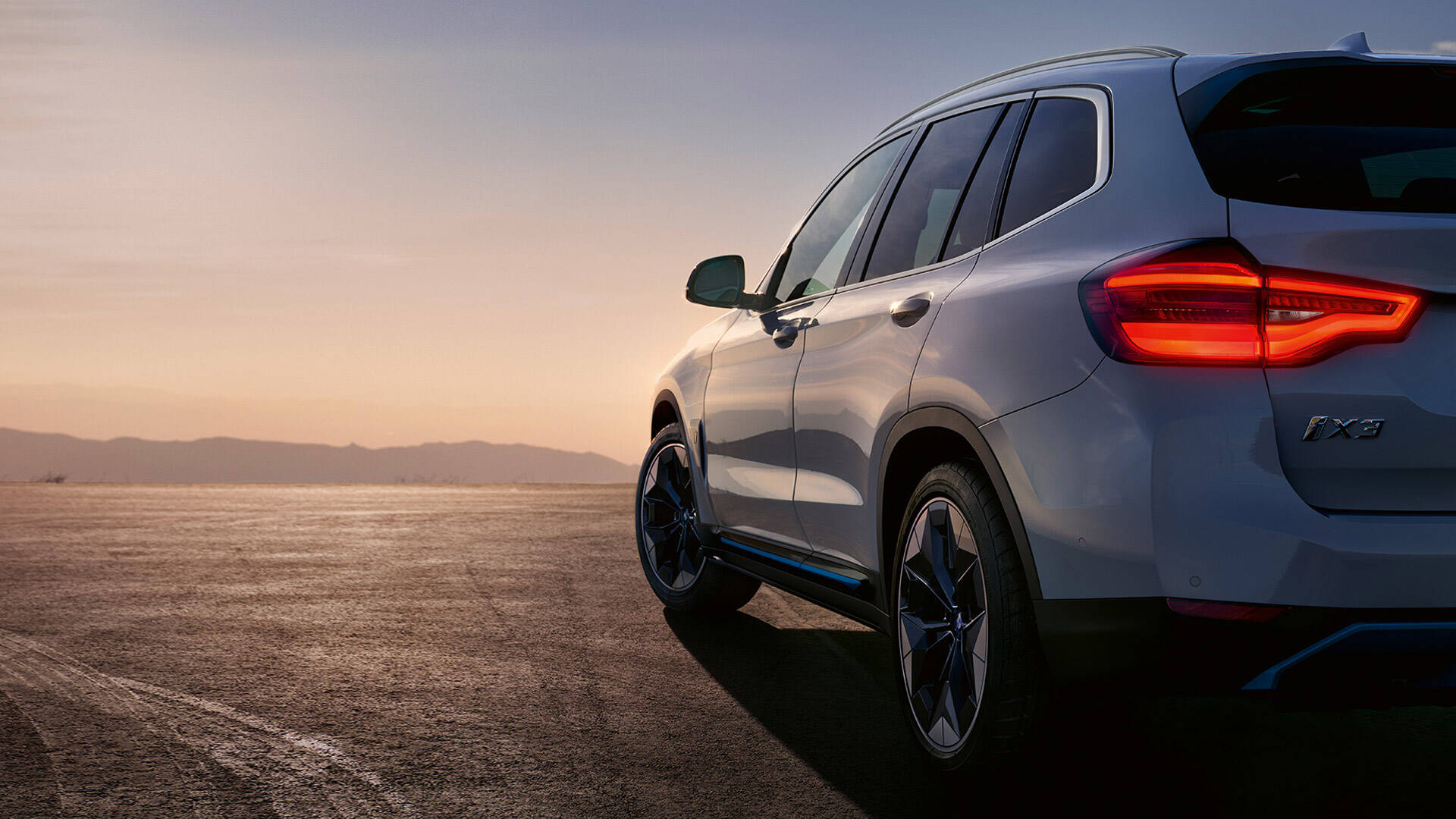
BMW Group is conducting pilot projects using digital tools, including blockchain technology, to track and control the global flow of goods.
The PartChain project, for example, makes it possible to collect supply chain data in a manner that is both consistent and fraud-proof. In the future, these digital technologies will enable us to track critical raw materials from source to reuse.
BLOCKCHAIN
We want to create transparency in recycling and reduce the usage of so-called virgin materials by re-using them on a large scale.
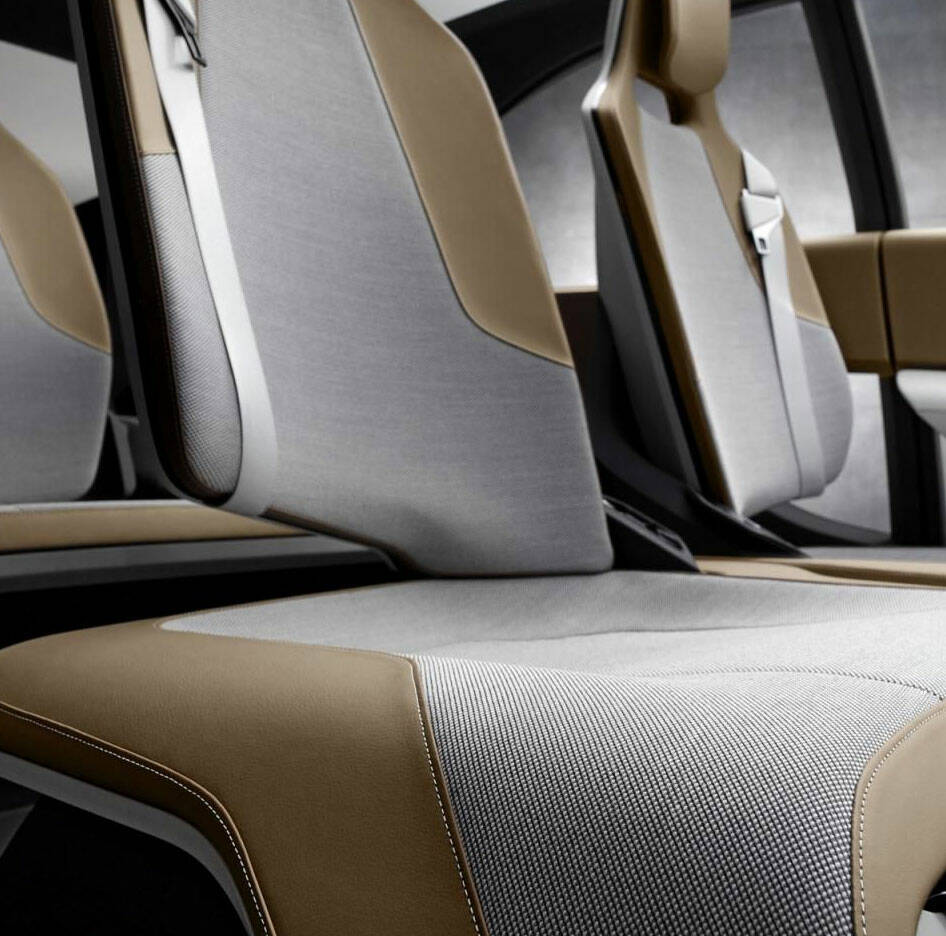